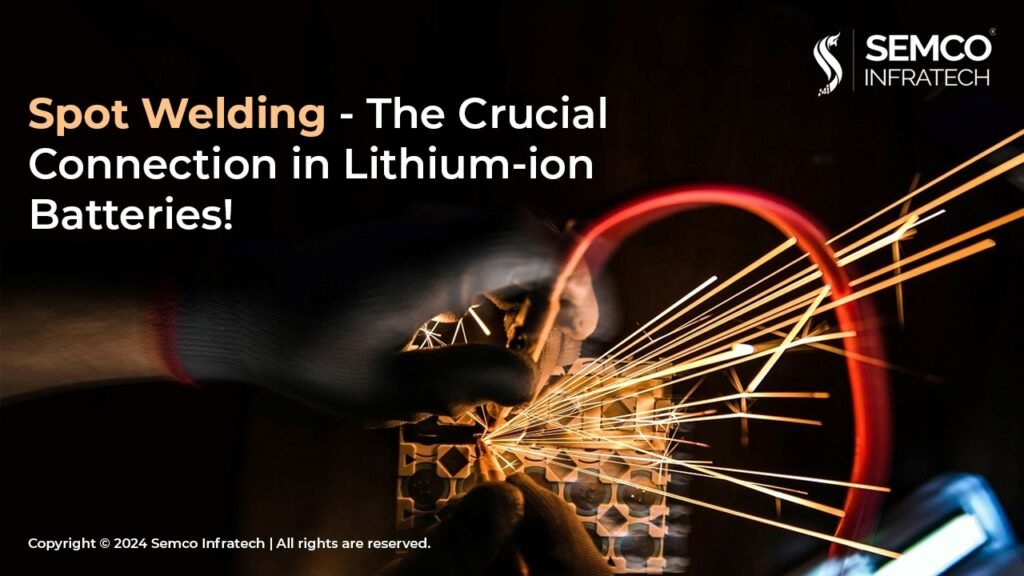
Modern technology relies on lithium-ion batteries to power everything from electric cars to laptops and smartphones. But for these batteries to work, there needs to be a secure electrical connection, which is where spot welding comes in.
Spot welding: what is it?
Spot welding is a kind of resistance welding in which two metal pieces are joined together locally by applying pressure and electrical current. A brief burst of high current is run through the metals’ overlapping surfaces during the process. The metals melt and fuse at the point of contact as a result of the localized heat produced by this strong current.
What is Spot Welding?
Spot welding is the recommended technique for joining parts of a lithium-ion battery because of several factors:
Precision: Precise welds are made possible by the localized heat generation, which doesn’t damage nearby materials. In the process of making batteries, this is vital because too much heat can harm delicate cell components.
Strength: Strong and dependable connections made with spot welds are resistant to the electrical and mechanical strains that batteries undergo while operating.
Speed and Efficiency: Spot welding is a quick and effective method that works well for production lines with large volumes.
Compatibility: The method functions effectively with the thin metal busbars and tabs that are frequently found in lithium-ion batteries.
Materials used in spot welding:
Electrodes: These are the conductive arms that provide the weld points with pressure and current application. Typically composed of copper because of its superior heat resistance and conductivity.
Tabs and Busbars: These are tiny metal strips that join the different battery cells in a pack together. Usually, nickel or nickel-plated steel is used to make them because of its excellent conductivity and weldability.
How is spot welding performed on lithium-ion batteries?
The process involves several steps:
Preparation: To guarantee proper electrical contact, the surfaces that need to be welded are cleaned and aligned.
Welding Parameters: The thickness of the material and the intended weld strength are taken into consideration when selecting the proper welding parameters, which include current, pulse duration, and electrode force.
Welding: The high current pulse is delivered, and the weld is formed by the electrodes pressing against the overlapping metal surfaces.
Cooling: The electrodes retract as the weld area cools.
Inspection: The weld joint is examined visually to ensure that it is properly formed and strong.
Safety considerations:
Lithium-ion batteries contain flammable electrolytes, making safety a paramount concern during spot welding. Some key safety measures include:
Proper ventilation: For the purpose of eliminating heat and fumes produced during welding, adequate ventilation is required.
Eye protection: To protect your eyes from sparks and spatter, put on the proper eye protection.
Safety protocols: Adhere to established safety protocols and procedures in order to reduce the likelihood of an explosion or fire.
Conclusion:
For lithium-ion batteries to operate dependably and effectively, spot welding is essential. For these essential components, its accuracy, speed, and compatibility make it the go-to joining technique. To ensure a safe and successful application in the production of lithium-ion batteries, however, appropriate safety precautions are necessary.