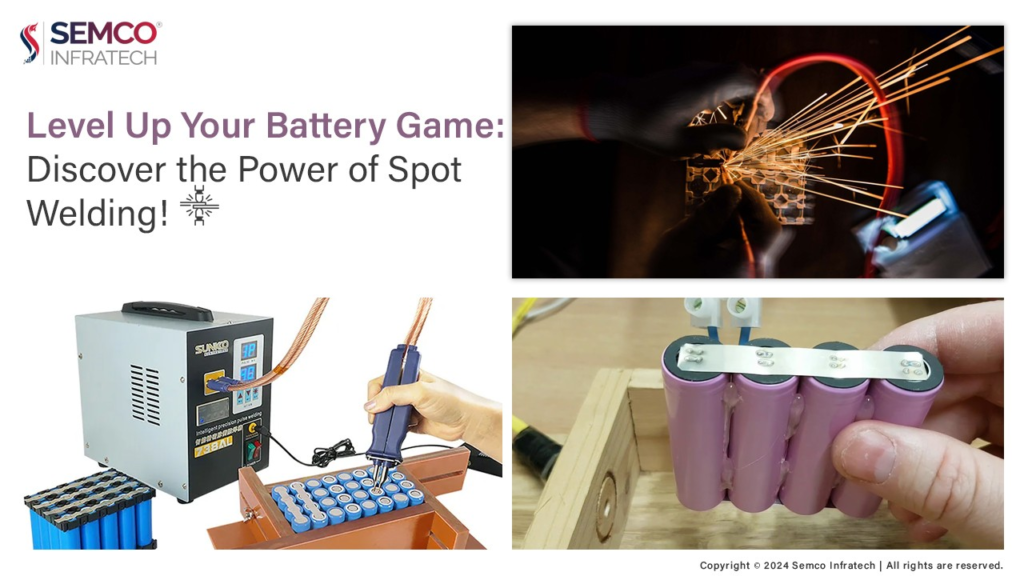
This article explains everything you need to know about lithium battery welding machines, essential tools for building lithium battery packs.
What is it?
A lithium battery welding machine (also called a spot welder) uses resistance welding to join lithium battery cells and terminals. It works by passing a current through the contact points, generating heat that melts solder to form a strong connection.
Key Parts:
- Welding Device: This core component includes the welding head, electrodes, and control system. Electrodes (often copper or chromium zirconium copper) come in various shapes and sizes for different applications. The control system ensures proper welding temperature and pressure.
- Power Supply: This system provides AC or DC power depending on welding needs.
- Cooling System: Keeps the welding device and power supply cool for optimal performance and lifespan.
- Auxiliary Components: Brackets, clamps, and workbenches hold and position batteries for precise welding.
How to Use It:
- Preparation: Gather batteries, solder sheets, and other materials. Position the batteries on the workbench.
- Welding Process: Place the welding piece between the electrodes, adjust pressure, and activate the machine. The heat melts the solder, creating a secure connection.
- Post-Welding: Check the weld quality and make adjustments if needed. Clean any residual solder for a tidy workspace.
Automated Process Flow:
Modern machines offer automated control. Users set parameters like welding path and battery formula through software. The machine then:
- Loads batteries and nickel sheets
- Positions them for welding
- Automatically aligns the welding needle
- Extends the welding head and initiates welding
- Sounds alarms for completion or faults
Benefits:
- Efficiency and Stability: Fast, reliable welding improves production speed.
- Wide Applicability: Works with various battery sizes and shapes with adjustable electrodes.
- Simple Operation: Automated control simplifies operation, minimizing human error.
- Easy Maintenance: The machine’s design allows for convenient maintenance.
- Safety and Reliability: Low voltage current reduces risks. Additional features like overcurrent and temperature protection enhance equipment safety.
- Economic Advantages: Boosts production efficiency, product quality, and reduces costs.
Important Considerations:
- Safe Operation: Operators should be trained and familiar with safety procedures. Regularly check the equipment’s safety features.
- Maintenance: Regular cleaning, part replacement (e.g., electrodes) is crucial for optimal performance and lifespan.
- Material Selection: Choose the right solder and soldering pieces for each application to avoid poor welding or equipment damage.
- Parameter Adjustment: Adjust electrode position, pressure, welding time, and temperature based on battery size and thickness for optimal welds.
- Quality Inspection: Always inspect welds after completion to identify weak or missing welds and make necessary adjustments.
- Work Environment: Maintain a clean and organized workspace free of dust and debris. Ensure proper operating temperature and humidity.
- Operator Training: Train new operators on basic operation, safety procedures, and how to improve their skills and work responsibly.
- Maintenance and Parts: Promptly repair equipment failures and keep spare parts readily available.
- Record Keeping: Maintain a log of equipment usage and maintenance to facilitate problem identification and resolution. Implement a traceability system to track equipment and quickly address production issues.
Conclusion:
Lithium battery welding machines are efficient, stable, and safe tools widely used in lithium battery production. Proper operation and maintenance ensure optimal equipment performance, leading to increased production efficiency, improved product quality, and reduced costs.