In the rapidly evolving world of lithium-ion battery manufacturing, laser welding technology stands out as a transformative innovation. As the demand for high-performance and energy-dense batteries continues to grow, particularly in sectors like electric vehicles (EVs) and renewable energy storage systems, the need for efficient and precise production methods has never been greater. In this blog, we uncover how laser welding technology is redefining battery production and shaping the future of sustainable energy solutions.
How Does Laser Welding Work in Lithium-Ion Battery Manufacturing?
Laser welding technology employs high-intensity laser beams to create strong and precise welds in critical battery components. This cutting-edge process minimizes the heat-affected zone, reducing thermal damage to sensitive materials. By focusing energy on targeted areas, laser welding technology ensures seamless connections between electrode foils, tabs, and other intricate components—enhancing both battery performance and durability.
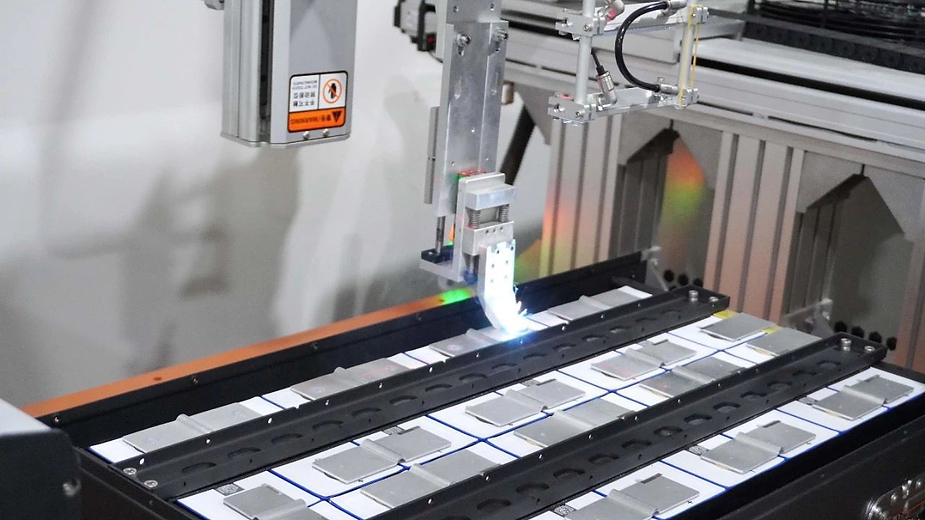
Industrial Applications of Laser Welding Technology
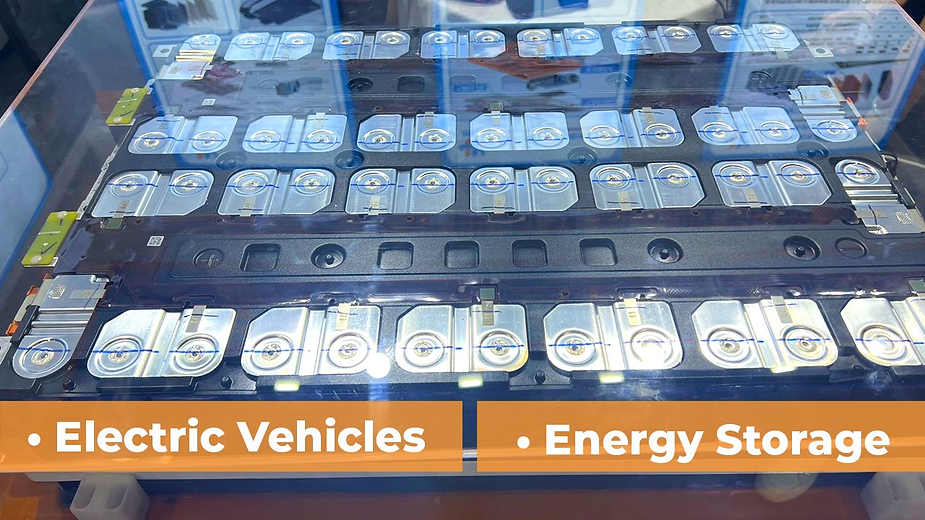
1. Electric Vehicles (EVs)
The global shift toward electric vehicles (EVs) has accelerated the demand for advanced battery manufacturing techniques. Laser welding technology’s speed and precision make it ideal for producing battery packs at scale, meeting the rigorous demands of EV manufacturers.
2. Energy Storage Systems
Renewable energy sources, like solar and wind, require efficient storage solutions to maintain grid stability. Lithium-ion batteries, manufactured using laser welding technology, play a crucial role in enabling grid-level energy storage systems and promoting the adoption of sustainable energy systems.
Key Advantages of Laser Welding in Battery Production
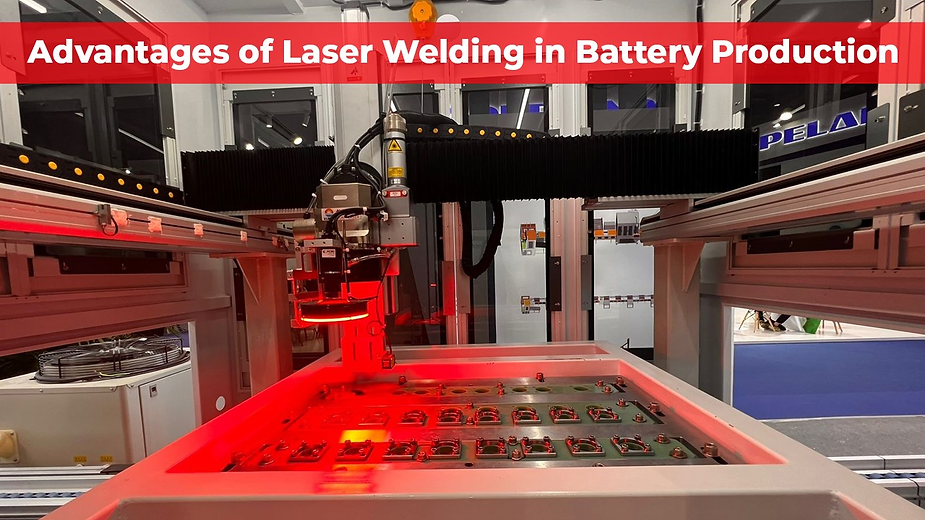
- Unmatched Precision
- Micron-level accuracy ensures consistent and reliable welds, even in complex battery designs.
- High-Speed Processing
- Laser welding technology’s rapid operation boosts production rates, catering to mass manufacturing needs.
- Minimal Heat Impact
- Reduced heat-affected zones protect sensitive materials, preserving the integrity of battery components.
- Low Maintenance Requirements
- The non-contact nature of laser welding technology minimizes wear and tear, reducing downtime and operational costs.
- Environmental Sustainability
- Laser welding technology eliminates the need for harmful chemicals or emissions, aligning with eco-friendly manufacturing practices.
Semco Laser Welding Machines: A Game-Changer in Manufacturing
The Semco Laser Welding Machine represents a leap forward in laser welding technology. Designed to handle a wide range of applications, it offers unparalleled versatility by catering to both metal and thermoplastic materials. During the welding process, the machine focuses a concentrated laser beam on a minute area, providing precise energy delivery. This approach ensures:
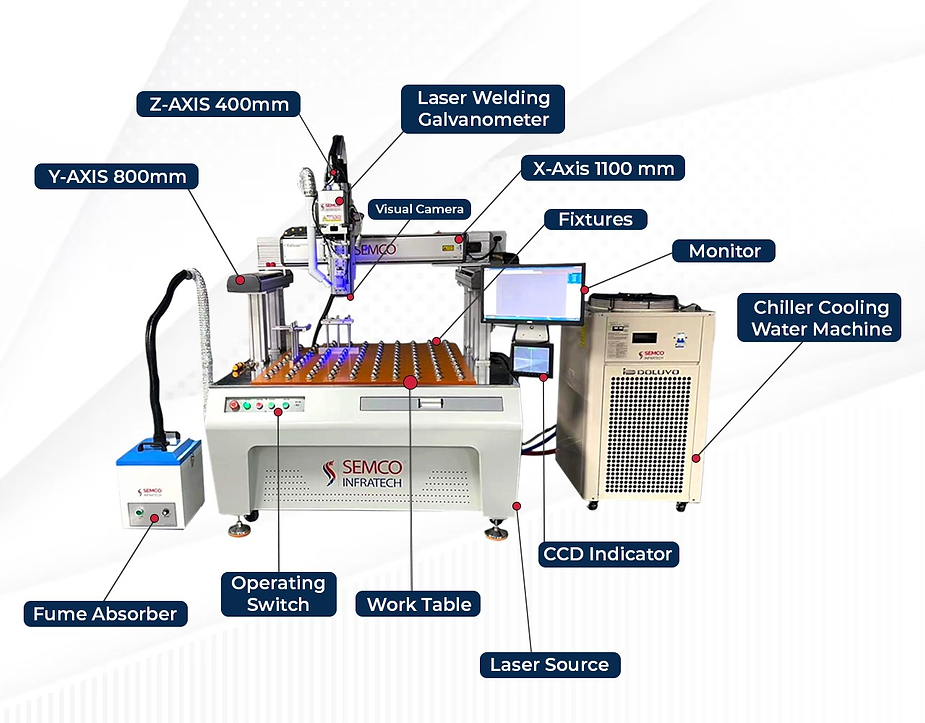
- Localized Heating: Minimizing material distortion and preserving metallurgical properties.
- Rapid Cooling: Preventing thermal damage to surrounding areas.
- Cost Efficiency: Reduced maintenance needs and energy usage lower operational costs.
Revolutionizing Industries with Laser Welding
Laser welding technology’s adaptability extends beyond battery manufacturing to diverse sectors, including E-mobility, aerospace, and consumer electronics. With its ability to meet stringent quality standards while enhancing production efficiency, laser welding technology is paving the way for innovation across industries.
Conclusion: Driving the Future of Precision Manufacturing
Laser welding technology is more than a manufacturing process; it’s a cornerstone of modern industrial innovation. By delivering precision, efficiency, and sustainability, laser welding technology is propelling industries toward new heights of progress. As the adoption of this technology expands, we can expect a brighter, more sustainable future powered by advanced lithium-ion batteries and other groundbreaking applications.
Embrace the future of battery manufacturing with Semco’s Laser Welding Machines—your partner in precision and performance.