Metal materials like copper and aluminum can be welded with a continuous fiber laser welding machine. For welding stability, the fuselage uses a high-strength gantry bed structure design. With its higher photoelectric conversion efficiency, lower power consumption, and higher beam quality, the current advanced continuous laser is chosen as the light source.
Benefits of the fiber laser apparatus include its small size, convenient use, and compact structure. Welding equipment can be efficiently integrated with other equipment in the system thanks to its versatile laser output mode. High speed and precision are ensured by the highly responsive servo motor output, which works with the high-precision and high-strength screw linear module as the operating transmission mechanism.
In the field of new energy lithium battery PACK modules, this makes the laser welding machine an essential piece of equipment. With its outstanding beam quality, quick welding speed, and gorgeous, sturdy welding pool, the continuous fiber laser welding machine offers the ideal, stable, and effective welding solution for the lithium battery welding process.
Unlocking the Advantages: Your Guide to the Equipment’s Benefits
- Perfect welding: Easy adjustment, fine focusing, imported optical lenses, high-precision laser welding head.
- High-quality fiber laser: Internationally recognized, with years of industrial application, a long lifespan, and no maintenance required.
- Energy efficiency: Low power consumption, high electro-optic conversion efficiency, and excellent beam quality.
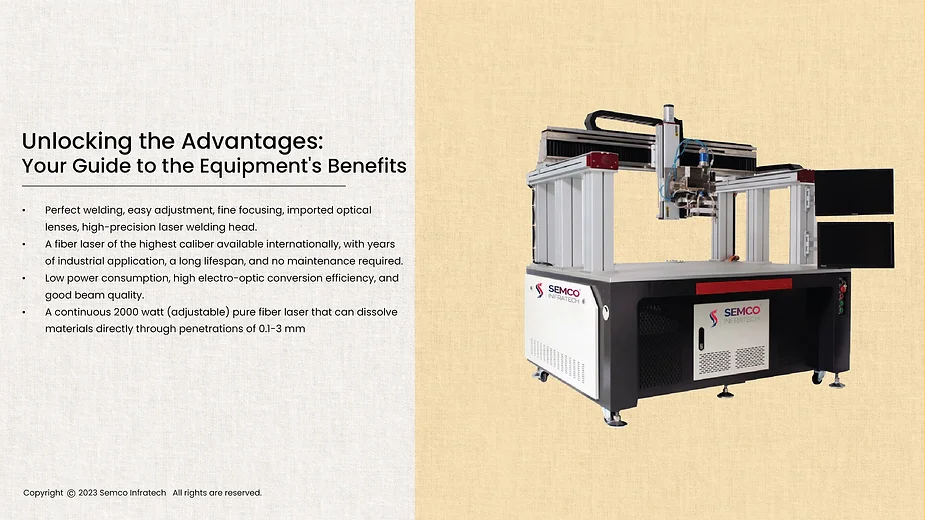
- Adjustable power: A continuous 2000-watt (adjustable) pure fiber laser that can penetrate materials with depths ranging from 0.1-3 mm.
- Precision control: A precise servo system ensures welding accuracy.
- User-friendly interface: Easy-to-learn PC industrial computer with a welding CNC programming system.
- Wide range capabilities: large surface stroke welding, a gantry frame motion structure, high machine tool precision, and a stable, long-lasting service life.
- Enhanced functionality: Data-saving call functions, strong drawing and editing graphics capabilities, and compatibility with a range of input formats.
Exploring Equipment Indicators and Parameters: Key Features
This welding equipment offers a range of features that make it versatile and reliable for various applications:
- Material Compatibility: Welds materials with thicknesses ranging from 0.5 mm to 2.0 mm, suitable for diverse projects.
- Workspace Flexibility: Effective travel range spans 870 mm in the X-axis and 600 mm in object workpiece height.

- Adjustable Welding Speed: Operates at speeds of up to 10 mm/s, ensuring welds meet specific requirements.
- Power Options: Offers adjustable laser power levels, including 2 KW, 3 KW, and 6 KW.
- Durability: Features an optical fiber working medium with a service life exceeding five years.
- Material Versatility: Suitable for welding nickel strips, copper sheets, and aluminum rows.
- Welding Modes: Offers both continuous and pulse modes for versatile welding processes.
- Spot Welding Capabilities: Achieves contact surface melting depths ranging from 0.5 mm to 1 mm, ensuring strong welds with tensile strength exceeding material destructive strength.
Characteristics of the Equipment
This welding equipment offers advantageous features for a seamless and efficient welding experience:
- Maintenance-Free Operation: Reduces downtime and maintenance costs.
- Adjustable Parameters: Allows for easy modification of welding parameters, including motion speed.
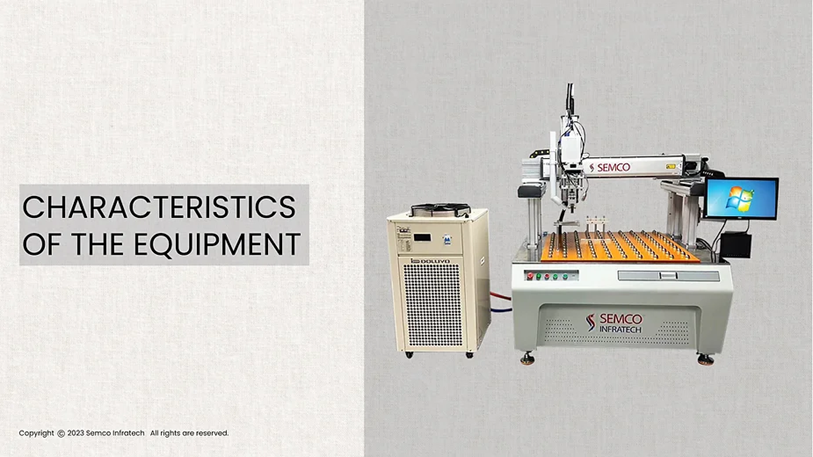
- Fault Alerts: Real-time fault alarm prompts for immediate issue resolution.
- Flexible Operation: Offers automatic and manual operation modes, supporting arc and straight-line interpolation.
- Laser Processing: Enables the creation of various plane graphics such as points, straight lines, circles, and squares.
- Durable Components: Equipped with imported lenses in the welding field mirror to withstand high laser-generated temperatures.
- User-Friendly System: Easy-to-learn operating system simplifies manual operation.
- Smoke and Slag Control: Built-in air-blown wind knife ensures welding quality.
- Cooling System: A water-cooled cycle in the welding head ensures stable welding effects.
- Precision Mechanism: High-precision screw transmission and high-speed servo motors ensure accuracy and responsiveness.
Environmental Conditions
To ensure optimal performance and safety, adhere to these specifications for the operating environment:
- Ambient Temperature: Operates effectively between 5°C and 35°C.
- Humidity: Maintain relative humidity levels between 20% and 90% to prevent condensation and corrosion.
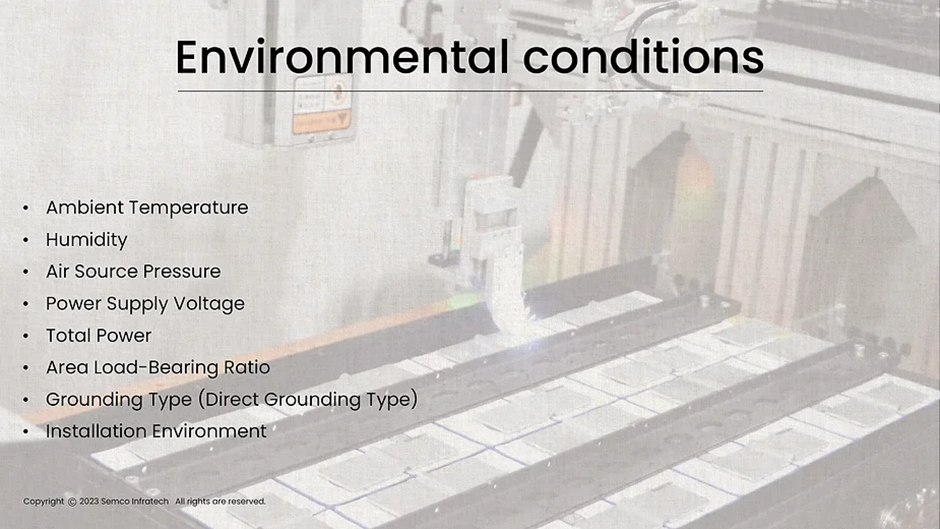
- Air Source Pressure: Requires a compressed air source with a pressure range of 0.5 to 0.6 Mpa.
- Power Supply Voltage: A stable voltage of 380V at 50Hz or 60Hz is required.
- Total Power: Consumes ≤10KW of power to prevent electrical overloading.
- Load-Bearing Capacity: The installation area must support up to 500 kg/m².
- Grounding Type: Direct grounding ensures safety and minimizes electrical hazards.
- Installation Environment: Requires a flat, vibration-free, and shock-free area for precise and stable operations.
Adhering to these specifications ensures reliable operation, extending the equipment’s service life while preventing potential issues related to environmental conditions.
Final Thoughts
The continuous fiber laser welding machine represents a revolutionary step forward in welding technology. Its ability to deliver precise, efficient, and versatile welding solutions makes it an essential tool across industries, including automotive, aerospace, and renewable energy. By understanding its functions, benefits, and operational requirements, manufacturers can fully leverage this equipment to enhance productivity, reduce costs, and achieve superior product quality.
Investing in a continuous fiber laser welding machine is not just about adopting advanced technology—it’s about future-proofing your manufacturing processes for the demands of tomorrow.