In the rapidly advancing world of new energy battery technology, ensuring the reliability and safety of battery packs is of paramount importance. One crucial aspect of this is conducting thorough stress and torque checks during the battery pack assembly process.
In this article, we will delve into a practical example of such checks, specifically focusing on the flange bolts of a module and the bottom of the output aluminum row.
Module Flange Bolt Installation Stress Check
The module’s structural integrity relies on the secure installation of its components, including flange bolts. In this example, four M6 studs are employed on each end plate of the module. The prescribed locking torque is set at 15+/-2N.m, with an upper limit of 17 for verification. To ensure safety, the torque is converted to a preload of 1467N.
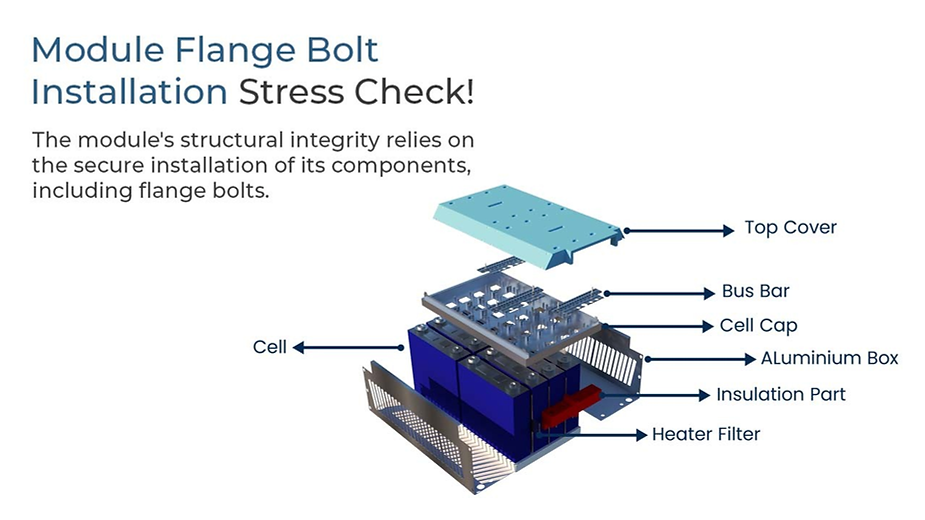
The first step is to measure the diameter of the flange surface, which is found to be 13.6mm, and the diameter of the end plate hole, measuring 8.2mm. With these measurements, we can calculate the pressing area (S) as follows: S = 3.14 x (6.8^2 – 4.1^2) = 92.4mm².
Now, we can calculate the stress applied to the end plate using the formula P = F/S = 14167/92.4/10^6 = 153.3Mpa. Considering the yield strength of the 6063-T6 material, which can be adjusted to 220Mpa, we find that 153.3Mpa comfortably meets the requirements, ensuring the structural integrity of the module.
Stress Check at the Bottom of the Output Aluminum Row
Similar to the flange bolts on the module, M6 flange surface bolts are used in this scenario. The prescribed locking torque is 13, which is converted to a preload of 10833N. The compression area is determined to be 103mm². Calculating the stress, we find P = F/S = 89Mpa. Comparing this value with the yield strength of the nickel sheet, which is 185Mpa, we can confirm that the stress levels are within acceptable limits, ensuring the reliability of the assembly.
Additional Tests and Considerations
In addition to torque and stress checks, there are several other critical tests and procedures that should be carried out during the battery pack assembly process. These include:
Insulation and Voltage Testing: Ensuring the insulation integrity and voltage levels within the pack are within safe limits.
Installation Torque Record: Recording and verifying the torque applied to various components for future reference.
Air Tightness Test of Liquid Cooling System: Checking for any leaks in the liquid cooling
system to prevent coolant loss.
Air Tightness Test of Battery Box: Ensuring that the battery box is sealed properly to prevent dust and moisture ingress.
Capacity Test: Verifying that the battery pack’s capacity matches the design specifications.
Adjusting the Shipment SOC: Setting the state-of-charge to an appropriate level for shipping and storage.
Brushing Software: Configuring the battery management system (BMS) software for optimal performance.
OCV Test: Conducting open circuit voltage tests to verify the pack’s voltage levels.
Weighing the Battery Pack: Measuring the weight of the fully assembled battery pack for documentation and transportation purposes.
The case study presented here emphasizes the importance of rigorous torque and stress checks in ensuring the reliability and safety of new energy battery packs. By following precise measurement and calculation procedures, manufacturers can confidently confirm that their battery modules and components are assembled to meet industry standards. Moreover, the implementation of additional tests and quality control measures further enhances the overall performance and safety of these critical energy storage systems.