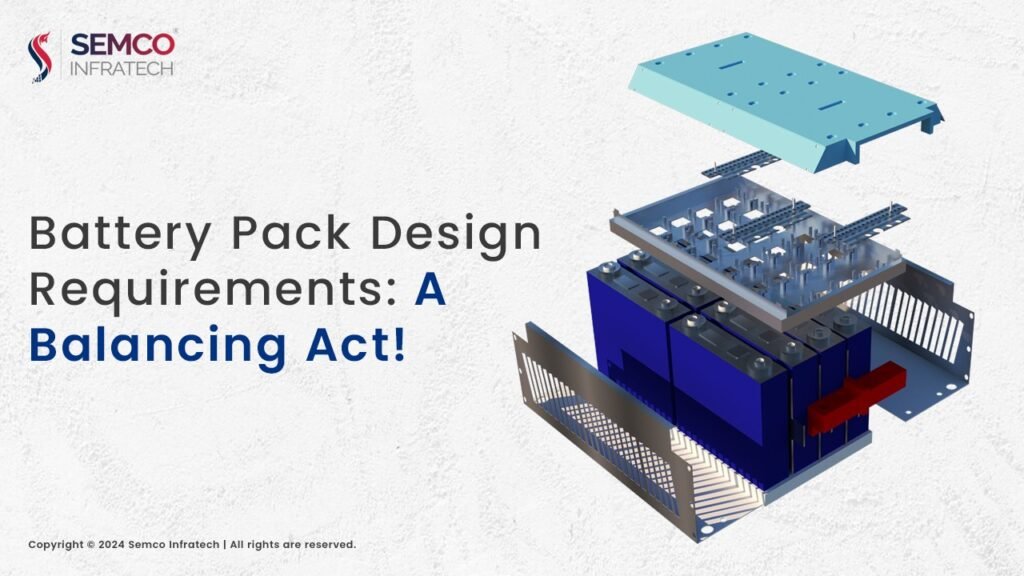
This article explores the key considerations for designing a battery pack for electric vehicles (EVs), focusing on four crucial aspects: mechanical, safety, maintenance, and cost.
1. Mechanical Requirements:
Shell Design: The shell forms the backbone of the battery pack, providing structural integrity and housing various components like modules, thermal management systems, and electrical interfaces.
Collision Performance: The shell needs to withstand potential collision forces, influencing its design and weight. Lighter shells are desirable for better driving range, but safety must not be compromised.
Environmental Protection: The casing requires an appropriate IP rating to protect against dust, water, corrosion, and road debris intrusion.
Electrical Isolation: High-voltage components like batteries and terminals must be electrically isolated from other conductive (low voltage) parts to prevent short circuits and ensure safety. Standards like ISO 6469-3 and IEC 60664-1 specify test procedures and design requirements for this purpose.
2. Safety Requirements:
Crashworthiness and Abuse Tolerance: Even with a strong shell, unexpected collisions can occur. The battery pack design must consider potential abuse situations like short circuits, overcharge, and penetration, ensuring safety and preventing thermal runaway in lithium-ion batteries.
Pressure Management: A pressure equalization system is crucial to handle any overpressure safely in case of battery venting.
Leakage Protection: The design should consider the potential leakage of the cooling system and its impact on the high-voltage system, preventing short circuits.
Electromagnetic Compatibility (EMC): The battery pack needs to comply with EMC regulations to minimize interference with other electronic systems in the vehicle.
Personnel Safety: Design features should prevent personnel from accessing hazardous high-voltage components.
3. Maintenance Requirements:
Serviceability: The battery pack design should consider the ease of replacing internal components during the EV’s service life. This includes facilitating recycling and potentially exploring second-life applications.
Repair Options: The design needs to accommodate the chosen service strategy. A centralized workshop approach allows for cost-effective component design, but requires additional costs for training technicians, tools, and transportation. Designing for wider service locations might necessitate more complex internal components but could offer logistical and training cost benefits.
4. Cost Requirements:
Cost Optimization: Given the high cost of lithium-ion batteries, all other components need to be designed in a cost-effective manner without compromising safety or durability.
Detailed Cost Analysis: A thorough cost analysis encompassing individual components, tooling, and development is crucial. Manufacturing methods for various components will be determined by the target production volume of battery packs.
Conclusion:
Designing an EV battery pack involves carefully balancing various requirements. Understanding these mechanical, safety, maintenance, and cost considerations is critical for creating a safe, reliable, and cost-effective solution that meets the demands of the electric vehicle market.